সেমিকন্ডাক্টর উৎপাদন প্রক্রিয়ার একটি গুরুত্বপূর্ণ ধাপ হিসেবে ওয়েফার ডাইসিং প্রযুক্তি সরাসরি চিপের কর্মক্ষমতা, ফলন এবং উৎপাদন খরচের সাথে যুক্ত।
#01 ওয়েফার ডাইসিংয়ের পটভূমি এবং তাৎপর্য
১.১ ওয়েফার ডাইসিংয়ের সংজ্ঞা
ওয়েফার ডাইসিং (যা স্ক্রাইবিং নামেও পরিচিত) সেমিকন্ডাক্টর উৎপাদনের একটি অপরিহার্য পদক্ষেপ, যার লক্ষ্য প্রক্রিয়াজাত ওয়েফারগুলিকে একাধিক পৃথক ডাইয়ে ভাগ করা। এই ডাইগুলিতে সাধারণত সম্পূর্ণ সার্কিট কার্যকারিতা থাকে এবং শেষ পর্যন্ত ইলেকট্রনিক ডিভাইস তৈরিতে ব্যবহৃত মূল উপাদান। চিপের নকশা যত জটিল হয়ে উঠছে এবং মাত্রা সঙ্কুচিত হচ্ছে, ওয়েফার ডাইসিং প্রযুক্তির জন্য নির্ভুলতা এবং দক্ষতার প্রয়োজনীয়তা ক্রমশ কঠোর হয়ে উঠছে।
ব্যবহারিক কাজে, ওয়েফার ডাইসিং সাধারণত উচ্চ-নির্ভুল সরঞ্জাম যেমন ডায়মন্ড ব্লেড ব্যবহার করে নিশ্চিত করা হয় যে প্রতিটি ডাই অক্ষত এবং সম্পূর্ণরূপে কার্যকর থাকে। মূল পদক্ষেপগুলির মধ্যে রয়েছে কাটার আগে প্রস্তুতি, কাটার প্রক্রিয়া চলাকালীন সুনির্দিষ্ট নিয়ন্ত্রণ এবং কাটার পরে গুণমান পরিদর্শন।
কাটার আগে, সঠিক কাটিংয়ের পথ নিশ্চিত করার জন্য ওয়েফারটি চিহ্নিত এবং স্থাপন করতে হবে। কাটার সময়, ওয়েফারের ক্ষতি রোধ করার জন্য সরঞ্জামের চাপ এবং গতির মতো পরামিতিগুলি কঠোরভাবে নিয়ন্ত্রণ করতে হবে। কাটার পরে, প্রতিটি চিপ কর্মক্ষমতা মান পূরণ করে কিনা তা নিশ্চিত করার জন্য ব্যাপক মানের পরিদর্শন করা হয়।
ওয়েফার ডাইসিং প্রযুক্তির মৌলিক নীতিগুলি কেবল কাটিয়া সরঞ্জাম নির্বাচন এবং প্রক্রিয়া পরামিতি নির্ধারণকেই অন্তর্ভুক্ত করে না, বরং কাটিয়া মানের উপর উপকরণের যান্ত্রিক বৈশিষ্ট্য এবং বৈশিষ্ট্যের প্রভাবকেও অন্তর্ভুক্ত করে। উদাহরণস্বরূপ, নিম্ন-কে ডাইইলেক্ট্রিক সিলিকন ওয়েফারগুলি, তাদের নিম্নমানের যান্ত্রিক বৈশিষ্ট্যের কারণে, কাটার সময় চাপ ঘনত্বের জন্য অত্যন্ত সংবেদনশীল, যার ফলে চিপিং এবং ফাটলের মতো ব্যর্থতা দেখা দেয়। কম-কে উপকরণগুলির কম কঠোরতা এবং ভঙ্গুরতা যান্ত্রিক বল বা তাপীয় চাপের অধীনে কাঠামোগত ক্ষতির ঝুঁকিতে ফেলে, বিশেষ করে কাটার সময়। উচ্চ তাপমাত্রার সাথে মিলিত হয়ে সরঞ্জাম এবং ওয়েফার পৃষ্ঠের মধ্যে যোগাযোগ চাপ ঘনত্বকে আরও বাড়িয়ে তুলতে পারে।
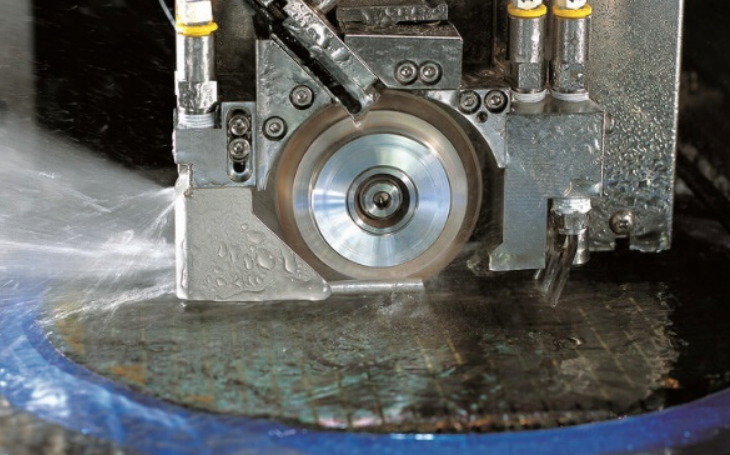
বস্তু বিজ্ঞানের অগ্রগতির সাথে সাথে, ওয়েফার ডাইসিং প্রযুক্তি ঐতিহ্যবাহী সিলিকন-ভিত্তিক সেমিকন্ডাক্টর ছাড়িয়ে গ্যালিয়াম নাইট্রাইড (GaN) এর মতো নতুন উপকরণ অন্তর্ভুক্ত করেছে। এই নতুন উপকরণগুলি, তাদের কঠোরতা এবং কাঠামোগত বৈশিষ্ট্যের কারণে, ডাইসিং প্রক্রিয়াগুলির জন্য নতুন চ্যালেঞ্জ তৈরি করে, যার জন্য কাটিয়া সরঞ্জাম এবং কৌশলগুলিতে আরও উন্নতির প্রয়োজন।
সেমিকন্ডাক্টর শিল্পে একটি গুরুত্বপূর্ণ প্রক্রিয়া হিসেবে, ক্রমবর্ধমান চাহিদা এবং প্রযুক্তিগত অগ্রগতির সাথে সাড়া দিয়ে ওয়েফার ডাইসিং অপ্টিমাইজ করা হচ্ছে, যা ভবিষ্যতের মাইক্রোইলেক্ট্রনিক্স এবং ইন্টিগ্রেটেড সার্কিট প্রযুক্তির ভিত্তি স্থাপন করে।
ওয়েফার ডাইসিং প্রযুক্তির উন্নতি কেবল সহায়ক উপকরণ এবং সরঞ্জামের উন্নয়নের বাইরেও বিস্তৃত। এর মধ্যে রয়েছে প্রক্রিয়া অপ্টিমাইজেশন, সরঞ্জামের কর্মক্ষমতা বৃদ্ধি এবং ডাইসিং পরামিতিগুলির সুনির্দিষ্ট নিয়ন্ত্রণ। এই অগ্রগতির লক্ষ্য হল ওয়েফার ডাইসিং প্রক্রিয়ায় উচ্চ নির্ভুলতা, দক্ষতা এবং স্থিতিশীলতা নিশ্চিত করা, যা সেমিকন্ডাক্টর শিল্পের ছোট মাত্রা, উচ্চতর ইন্টিগ্রেশন এবং আরও জটিল চিপ কাঠামোর চাহিদা পূরণ করে।
উন্নয়ন এলাকা | নির্দিষ্ট ব্যবস্থা | প্রভাব |
প্রক্রিয়া অপ্টিমাইজেশন | - প্রাথমিক প্রস্তুতি উন্নত করুন, যেমন আরও সঠিক ওয়েফার পজিশনিং এবং পথ পরিকল্পনা। | - কাটার ত্রুটি হ্রাস করুন এবং স্থায়িত্ব উন্নত করুন। |
- কাটার ত্রুটি কমিয়ে আনুন এবং স্থায়িত্ব বাড়ান। | - টুলের চাপ, গতি এবং তাপমাত্রা সামঞ্জস্য করতে রিয়েল-টাইম পর্যবেক্ষণ এবং প্রতিক্রিয়া প্রক্রিয়া গ্রহণ করুন। | |
- ওয়েফার ভাঙনের হার কমানো এবং চিপের মান উন্নত করা। | ||
সরঞ্জামের কর্মক্ষমতা বৃদ্ধি | - উচ্চ-নির্ভুল যান্ত্রিক সিস্টেম এবং উন্নত অটোমেশন নিয়ন্ত্রণ প্রযুক্তি ব্যবহার করুন। | - কাটার নির্ভুলতা বৃদ্ধি করুন এবং উপাদানের অপচয় কমান। |
- উচ্চ-কঠোরতা উপাদান ওয়েফারের জন্য উপযুক্ত লেজার কাটিং প্রযুক্তি প্রবর্তন করুন। | - উৎপাদন দক্ষতা উন্নত করুন এবং ম্যানুয়াল ত্রুটি কমান। | |
- স্বয়ংক্রিয় পর্যবেক্ষণ এবং সমন্বয়ের জন্য সরঞ্জামের অটোমেশন বৃদ্ধি করুন। | ||
সুনির্দিষ্ট প্যারামিটার নিয়ন্ত্রণ | - কাটার গভীরতা, গতি, টুলের ধরণ এবং শীতলকরণ পদ্ধতির মতো পরামিতিগুলি সূক্ষ্মভাবে সামঞ্জস্য করুন। | - ডাই অখণ্ডতা এবং বৈদ্যুতিক কর্মক্ষমতা নিশ্চিত করুন। |
- ওয়েফার উপাদান, বেধ এবং গঠনের উপর ভিত্তি করে পরামিতিগুলি কাস্টমাইজ করুন। | - উৎপাদনের হার বৃদ্ধি করুন, উপাদানের অপচয় কম করুন এবং উৎপাদন খরচ কম করুন। | |
কৌশলগত তাৎপর্য | - বাজারের চাহিদা মেটাতে ক্রমাগত নতুন প্রযুক্তিগত পথ অন্বেষণ করুন, প্রক্রিয়াগুলি অপ্টিমাইজ করুন এবং সরঞ্জামের ক্ষমতা বৃদ্ধি করুন। | - নতুন উপকরণ এবং উন্নত চিপ ডিজাইনের উন্নয়নে সহায়তা করে, চিপ উৎপাদনের ফলন এবং কর্মক্ষমতা উন্নত করুন। |
১.২ ওয়েফার ডাইসিংয়ের গুরুত্ব
সেমিকন্ডাক্টর উৎপাদন প্রক্রিয়ায় ওয়েফার ডাইসিং একটি গুরুত্বপূর্ণ ভূমিকা পালন করে, যা পরবর্তী ধাপগুলির পাশাপাশি চূড়ান্ত পণ্যের গুণমান এবং কর্মক্ষমতার উপর সরাসরি প্রভাব ফেলে। এর গুরুত্ব নিম্নরূপে বিশদভাবে বর্ণনা করা যেতে পারে:
প্রথমত, ডাইসিংয়ের নির্ভুলতা এবং ধারাবাহিকতা চিপের ফলন এবং নির্ভরযোগ্যতা নিশ্চিত করার মূল চাবিকাঠি। উৎপাদনের সময়, ওয়েফারগুলিকে একাধিক প্রক্রিয়াকরণ ধাপ অতিক্রম করতে হয় যাতে অসংখ্য জটিল সার্কিট কাঠামো তৈরি হয়, যেগুলিকে অবশ্যই পৃথক চিপগুলিতে (ডাই) বিভক্ত করতে হয়। ডাইসিং প্রক্রিয়া চলাকালীন যদি অ্যালাইনমেন্ট বা কাটার ক্ষেত্রে উল্লেখযোগ্য ত্রুটি থাকে, তাহলে সার্কিটগুলি ক্ষতিগ্রস্ত হতে পারে, যা চিপের কার্যকারিতা এবং নির্ভরযোগ্যতাকে প্রভাবিত করে। অতএব, উচ্চ-নির্ভুল ডাইসিং প্রযুক্তি কেবল প্রতিটি চিপের অখণ্ডতা নিশ্চিত করে না বরং অভ্যন্তরীণ সার্কিটের ক্ষতিও প্রতিরোধ করে, সামগ্রিক ফলন হার উন্নত করে।
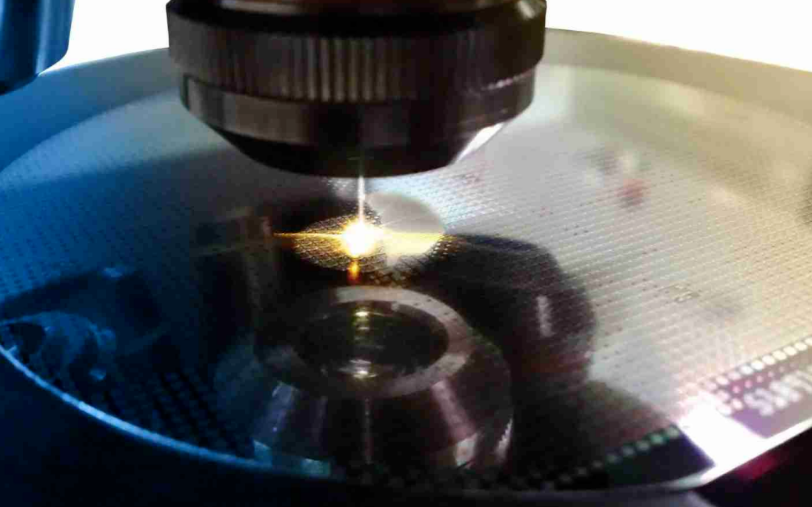
দ্বিতীয়ত, ওয়েফার ডাইসিং উৎপাদন দক্ষতা এবং খরচ নিয়ন্ত্রণের উপর উল্লেখযোগ্য প্রভাব ফেলে। উৎপাদন প্রক্রিয়ার একটি গুরুত্বপূর্ণ পদক্ষেপ হিসেবে, এর দক্ষতা সরাসরি পরবর্তী পদক্ষেপগুলির অগ্রগতিকে প্রভাবিত করে। ডাইসিং প্রক্রিয়াটি অপ্টিমাইজ করে, অটোমেশনের মাত্রা বৃদ্ধি করে এবং কাটিংয়ের গতি উন্নত করে, সামগ্রিক উৎপাদন দক্ষতা ব্যাপকভাবে বৃদ্ধি করা যেতে পারে।
অন্যদিকে, ডাইসিংয়ের সময় উপাদানের অপচয় খরচ ব্যবস্থাপনার একটি গুরুত্বপূর্ণ বিষয়। উন্নত ডাইসিং প্রযুক্তি ব্যবহার কেবল কাটার প্রক্রিয়ার সময় অপ্রয়োজনীয় উপাদানের ক্ষতি হ্রাস করে না বরং ওয়েফারের ব্যবহারও বৃদ্ধি করে, যার ফলে উৎপাদন খরচ কম হয়।
সেমিকন্ডাক্টর প্রযুক্তির অগ্রগতির সাথে সাথে, ওয়েফারের ব্যাস বৃদ্ধি পাচ্ছে এবং সার্কিটের ঘনত্ব সেই অনুযায়ী বৃদ্ধি পাচ্ছে, যার ফলে ডাইসিং প্রযুক্তির চাহিদা বেশি। বৃহৎ ওয়েফারের জন্য কাটিংয়ের পথের আরও সুনির্দিষ্ট নিয়ন্ত্রণ প্রয়োজন, বিশেষ করে উচ্চ-ঘনত্বের সার্কিট এলাকায়, যেখানে সামান্য বিচ্যুতিও একাধিক চিপকে ত্রুটিপূর্ণ করে তুলতে পারে। অতিরিক্তভাবে, বৃহৎ ওয়েফারগুলিতে আরও কাটিংয়ের লাইন এবং আরও জটিল প্রক্রিয়া পদক্ষেপ জড়িত, যা এই চ্যালেঞ্জগুলি মোকাবেলা করার জন্য ডাইসিং প্রযুক্তির নির্ভুলতা, ধারাবাহিকতা এবং দক্ষতায় আরও উন্নতির প্রয়োজন।
১.৩ ওয়েফার ডাইসিং প্রক্রিয়া
ওয়েফার ডাইসিং প্রক্রিয়া প্রস্তুতির পর্যায় থেকে চূড়ান্ত মান পরিদর্শন পর্যন্ত সমস্ত ধাপকে অন্তর্ভুক্ত করে, প্রতিটি ধাপ ডাইস করা চিপগুলির গুণমান এবং কর্মক্ষমতা নিশ্চিত করার জন্য অত্যন্ত গুরুত্বপূর্ণ। নীচে প্রতিটি ধাপের বিস্তারিত ব্যাখ্যা দেওয়া হল।
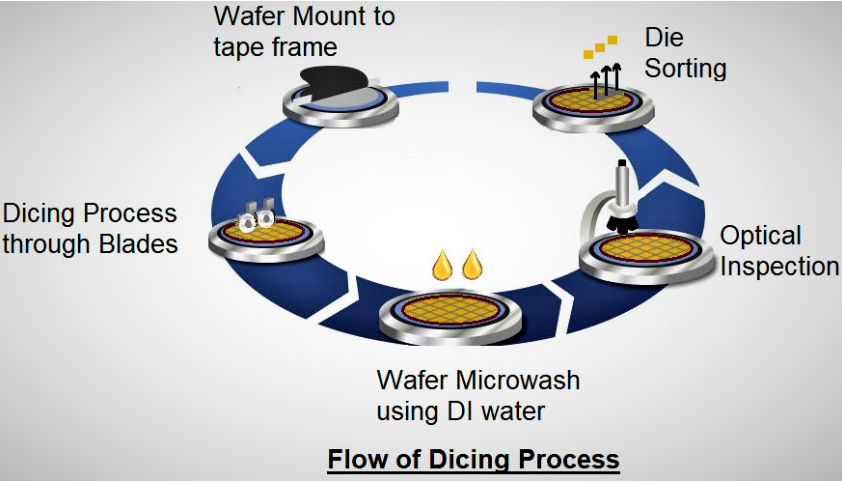
পর্যায় | বিস্তারিত বিবরণ |
প্রস্তুতির পর্যায় | -ওয়েফার পরিষ্কার: উচ্চ-বিশুদ্ধতা সম্পন্ন জল এবং বিশেষায়িত পরিষ্কারক এজেন্ট ব্যবহার করুন, অতিস্বনক বা যান্ত্রিক স্ক্রাবিংয়ের সাথে মিলিত হয়ে, অমেধ্য, কণা এবং দূষক অপসারণ করুন, যাতে পৃষ্ঠ পরিষ্কার থাকে। -সুনির্দিষ্ট অবস্থান নির্ধারণ: ডিজাইন করা কাটিং পাথ বরাবর ওয়েফারটি সঠিকভাবে বিভক্ত হয়েছে তা নিশ্চিত করতে উচ্চ-নির্ভুল সরঞ্জাম ব্যবহার করুন। -ওয়েফার ফিক্সেশন: কাটার সময় স্থিতিশীলতা বজায় রাখার জন্য, কম্পন বা নড়াচড়ার কারণে ক্ষতি রোধ করার জন্য ওয়েফারটিকে একটি টেপ ফ্রেমের উপর সুরক্ষিত করুন। |
কাটিং ফেজ | -ব্লেড ডাইসিং: সিলিকন-ভিত্তিক উপকরণের জন্য উপযুক্ত এবং সাশ্রয়ী মূল্যের, ভৌত কাটার জন্য উচ্চ-গতির ঘূর্ণায়মান হীরা-প্রলিপ্ত ব্লেড ব্যবহার করুন। -লেজার ডাইসিং: যোগাযোগহীন কাটার জন্য উচ্চ-শক্তির লেজার রশ্মি ব্যবহার করুন, যা গ্যালিয়াম নাইট্রাইডের মতো ভঙ্গুর বা উচ্চ-কঠোরতা উপাদানের জন্য আদর্শ, যা উচ্চ নির্ভুলতা এবং কম উপাদানের ক্ষতি প্রদান করে। -নতুন প্রযুক্তি: তাপ-প্রভাবিত অঞ্চলগুলিকে কমিয়ে আনার সাথে সাথে দক্ষতা এবং নির্ভুলতা আরও উন্নত করতে লেজার এবং প্লাজমা কাটিং প্রযুক্তি প্রবর্তন করুন। |
পরিষ্কারের পর্যায় | - কাটার সময় উৎপন্ন ধ্বংসাবশেষ এবং ধুলো অপসারণের জন্য ডিওনাইজড ওয়াটার (ডিআই ওয়াটার) এবং বিশেষায়িত পরিষ্কারক এজেন্ট ব্যবহার করুন, যা অতিস্বনক বা স্প্রে পরিষ্কারের সাথে মিলিত হয়, যা পরবর্তী প্রক্রিয়াগুলিকে প্রভাবিত করতে বা বৈদ্যুতিক কর্মক্ষমতা চিপ করতে অবশিষ্টাংশগুলিকে বাধা দেয়। - উচ্চ-বিশুদ্ধতা DI জল নতুন দূষণকারী পদার্থের প্রবেশ এড়ায়, একটি পরিষ্কার ওয়েফার পরিবেশ নিশ্চিত করে। |
পরিদর্শন পর্যায় | -অপটিক্যাল পরিদর্শন: ত্রুটিগুলি দ্রুত সনাক্ত করতে, কাটা চিপগুলিতে কোনও ফাটল বা চিপিং না হওয়া নিশ্চিত করতে, পরিদর্শন দক্ষতা উন্নত করতে এবং মানুষের ত্রুটি হ্রাস করতে AI অ্যালগরিদমের সাথে মিলিত অপটিক্যাল সনাক্তকরণ সিস্টেম ব্যবহার করুন। -মাত্রা পরিমাপ: চিপের মাত্রা ডিজাইনের স্পেসিফিকেশন পূরণ করে কিনা তা যাচাই করুন। -বৈদ্যুতিক কর্মক্ষমতা পরীক্ষা: নিশ্চিত করুন যে গুরুত্বপূর্ণ চিপগুলির বৈদ্যুতিক কর্মক্ষমতা মান পূরণ করে, পরবর্তী প্রয়োগগুলিতে নির্ভরযোগ্যতা নিশ্চিত করে। |
বাছাই পর্ব | - টেপ ফ্রেম থেকে যোগ্য চিপগুলি আলাদা করতে রোবোটিক আর্ম বা ভ্যাকুয়াম সাকশন কাপ ব্যবহার করুন এবং কর্মক্ষমতার উপর ভিত্তি করে স্বয়ংক্রিয়ভাবে সেগুলি বাছাই করুন, উৎপাদন দক্ষতা এবং নমনীয়তা নিশ্চিত করার সাথে সাথে নির্ভুলতা উন্নত করুন। |
ওয়েফার কাটার প্রক্রিয়ায় ওয়েফার পরিষ্কার, অবস্থান নির্ধারণ, কাটা, পরিষ্কার, পরিদর্শন এবং বাছাই জড়িত, প্রতিটি ধাপ অত্যন্ত গুরুত্বপূর্ণ। অটোমেশন, লেজার কাটিং এবং এআই পরিদর্শন প্রযুক্তির অগ্রগতির সাথে সাথে, আধুনিক ওয়েফার কাটিং সিস্টেমগুলি উচ্চতর নির্ভুলতা, গতি এবং কম উপাদানের ক্ষতি অর্জন করতে পারে। ভবিষ্যতে, লেজার এবং প্লাজমার মতো নতুন কাটিং প্রযুক্তি ধীরে ধীরে ক্রমবর্ধমান জটিল চিপ ডিজাইনের চাহিদা পূরণের জন্য ঐতিহ্যবাহী ব্লেড কাটিংকে প্রতিস্থাপন করবে, যা সেমিকন্ডাক্টর উৎপাদন প্রক্রিয়ার বিকাশকে আরও ত্বরান্বিত করবে।
ওয়েফার কাটিং প্রযুক্তি এবং এর নীতিমালা
ছবিটি তিনটি সাধারণ ওয়েফার কাটার প্রযুক্তি চিত্রিত করে:ব্লেড ডাইসিং,লেজার ডাইসিং, এবংপ্লাজমা ডাইসিংনিচে এই তিনটি কৌশলের বিস্তারিত বিশ্লেষণ এবং পরিপূরক ব্যাখ্যা দেওয়া হল:
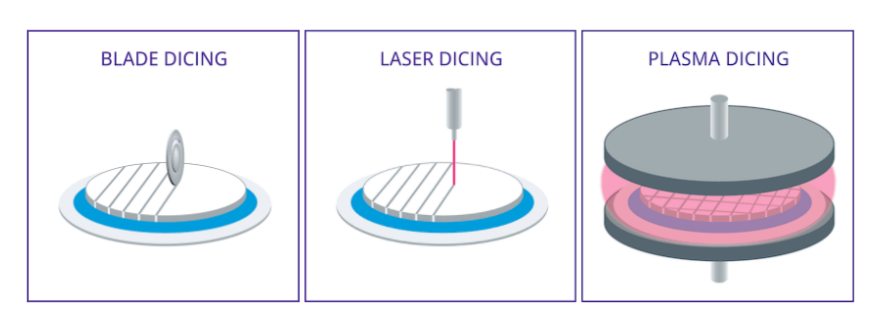
সেমিকন্ডাক্টর উৎপাদনে, ওয়েফার কাটিং একটি গুরুত্বপূর্ণ পদক্ষেপ যার জন্য ওয়েফারের পুরুত্বের উপর ভিত্তি করে উপযুক্ত কাটিং পদ্ধতি নির্বাচন করা প্রয়োজন। প্রথম ধাপ হল ওয়েফারের পুরুত্ব নির্ধারণ করা। যদি ওয়েফারের পুরুত্ব ১০০ মাইক্রনের বেশি হয়, তাহলে ব্লেড ডাইসিংকে কাটিং পদ্ধতি হিসেবে বেছে নেওয়া যেতে পারে। যদি ব্লেড ডাইসিং উপযুক্ত না হয়, তাহলে ফ্র্যাকচার ডাইসিং পদ্ধতি ব্যবহার করা যেতে পারে, যার মধ্যে স্ক্রাইব কাটিং এবং ব্লেড ডাইসিং উভয় কৌশল অন্তর্ভুক্ত থাকে।
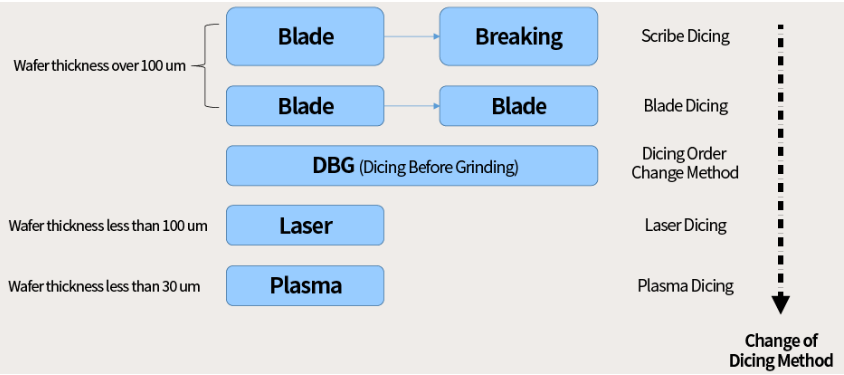
যখন ওয়েফারের পুরুত্ব 30 থেকে 100 মাইক্রনের মধ্যে হয়, তখন DBG (ডাইস বিফোর গ্রাইন্ডিং) পদ্ধতিটি সুপারিশ করা হয়। এই ক্ষেত্রে, সেরা ফলাফল অর্জনের জন্য স্ক্রাইব কাটিং, ব্লেড ডাইসিং, অথবা প্রয়োজন অনুসারে কাটিং সিকোয়েন্স সামঞ্জস্য করা বেছে নেওয়া যেতে পারে।
৩০ মাইক্রনের কম পুরুত্বের অতি-পাতলা ওয়েফারের জন্য, লেজার কাটিং পছন্দের পদ্ধতি হয়ে ওঠে কারণ এটি অতিরিক্ত ক্ষতি না করে পাতলা ওয়েফারগুলিকে সঠিকভাবে কাটতে পারে। যদি লেজার কাটিং নির্দিষ্ট প্রয়োজনীয়তা পূরণ করতে না পারে, তাহলে বিকল্প হিসেবে প্লাজমা কাটিং ব্যবহার করা যেতে পারে। এই ফ্লোচার্টটি বিভিন্ন পুরুত্বের পরিস্থিতিতে সবচেয়ে উপযুক্ত ওয়েফার কাটিং প্রযুক্তি বেছে নেওয়ার জন্য একটি স্পষ্ট সিদ্ধান্ত গ্রহণের পথ প্রদান করে।
২.১ যান্ত্রিক কাটিং প্রযুক্তি
ওয়েফার ডাইসিংয়ের ঐতিহ্যবাহী পদ্ধতি হল যান্ত্রিক কাটিয়া প্রযুক্তি। মূল নীতি হল ওয়েফার কাটার জন্য একটি উচ্চ-গতির ঘূর্ণায়মান হীরা গ্রাইন্ডিং চাকা ব্যবহার করা। মূল সরঞ্জামগুলির মধ্যে একটি বায়ু-বহনকারী স্পিন্ডল রয়েছে, যা একটি পূর্বনির্ধারিত কাটিয়া পথ ধরে সুনির্দিষ্ট কাটিয়া বা খাঁজকাটা সম্পাদনের জন্য উচ্চ গতিতে হীরা গ্রাইন্ডিং চাকা সরঞ্জামটি চালিত করে। কম খরচ, উচ্চ দক্ষতা এবং ব্যাপক প্রযোজ্যতার কারণে এই প্রযুক্তিটি শিল্পে ব্যাপকভাবে ব্যবহৃত হয়।
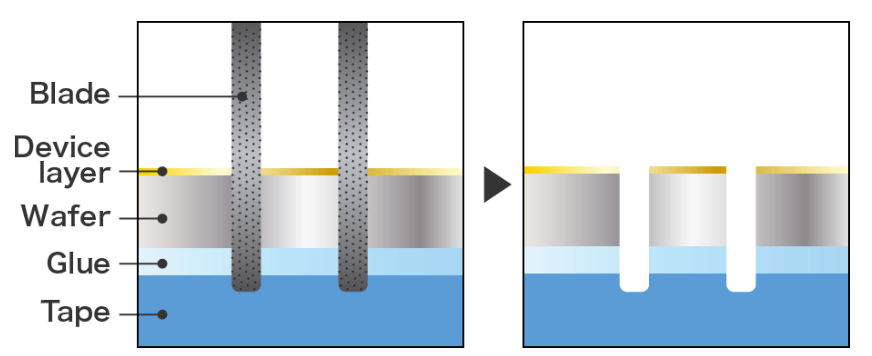
সুবিধাদি
হীরা গ্রাইন্ডিং হুইল টুলের উচ্চ কঠোরতা এবং পরিধান প্রতিরোধ ক্ষমতা যান্ত্রিক কাটিয়া প্রযুক্তিকে বিভিন্ন ওয়েফার উপকরণের কাটিয়া চাহিদার সাথে খাপ খাইয়ে নিতে সক্ষম করে, তা সে ঐতিহ্যবাহী সিলিকন-ভিত্তিক উপকরণ হোক বা নতুন যৌগিক সেমিকন্ডাক্টর। এর কার্যকারিতা সহজ, তুলনামূলকভাবে কম প্রযুক্তিগত প্রয়োজনীয়তা সহ, যা ব্যাপক উৎপাদনে এর জনপ্রিয়তাকে আরও বাড়িয়ে তোলে। উপরন্তু, লেজার কাটার মতো অন্যান্য কাটিয়া পদ্ধতির তুলনায়, যান্ত্রিক কাটিয়া খরচ বেশি নিয়ন্ত্রণযোগ্য, যা এটিকে উচ্চ-ভলিউম উৎপাদন চাহিদার জন্য উপযুক্ত করে তোলে।
সীমাবদ্ধতা
অসংখ্য সুবিধা থাকা সত্ত্বেও, যান্ত্রিক কাটিয়া প্রযুক্তিরও সীমাবদ্ধতা রয়েছে। প্রথমত, সরঞ্জাম এবং ওয়েফারের মধ্যে শারীরিক যোগাযোগের কারণে, কাটার নির্ভুলতা তুলনামূলকভাবে সীমিত, যা প্রায়শই মাত্রিক বিচ্যুতির দিকে পরিচালিত করে যা পরবর্তী চিপ প্যাকেজিং এবং পরীক্ষার নির্ভুলতাকে প্রভাবিত করতে পারে। দ্বিতীয়ত, যান্ত্রিক কাটিয়া প্রক্রিয়ার সময় চিপিং এবং ফাটলের মতো ত্রুটিগুলি সহজেই ঘটতে পারে, যা কেবল ফলনের হারকেই প্রভাবিত করে না বরং চিপগুলির নির্ভরযোগ্যতা এবং জীবনকালকেও নেতিবাচকভাবে প্রভাবিত করতে পারে। যান্ত্রিক চাপ-প্ররোচিত ক্ষতি উচ্চ-ঘনত্বের চিপ উত্পাদনের জন্য বিশেষভাবে ক্ষতিকারক, বিশেষ করে ভঙ্গুর উপকরণ কাটার সময়, যেখানে এই সমস্যাগুলি আরও স্পষ্ট।
প্রযুক্তিগত উন্নতি
এই সীমাবদ্ধতাগুলি কাটিয়ে ওঠার জন্য, গবেষকরা ক্রমাগত যান্ত্রিক কাটিয়া প্রক্রিয়াটি অপ্টিমাইজ করছেন। মূল উন্নতিগুলির মধ্যে রয়েছে কাটার নির্ভুলতা এবং স্থায়িত্ব উন্নত করার জন্য গ্রাইন্ডিং চাকার নকশা এবং উপাদান নির্বাচন বৃদ্ধি করা। উপরন্তু, কাটিয়া সরঞ্জামের কাঠামোগত নকশা এবং নিয়ন্ত্রণ ব্যবস্থা অপ্টিমাইজ করার ফলে কাটিয়া প্রক্রিয়ার স্থায়িত্ব এবং স্বয়ংক্রিয়তা আরও উন্নত হয়েছে। এই অগ্রগতিগুলি মানুষের ক্রিয়াকলাপের ফলে সৃষ্ট ত্রুটি হ্রাস করে এবং কাটিয়াগুলির ধারাবাহিকতা উন্নত করে। কাটিয়া প্রক্রিয়া চলাকালীন অসঙ্গতিগুলির রিয়েল-টাইম পর্যবেক্ষণের জন্য উন্নত পরিদর্শন এবং মান নিয়ন্ত্রণ প্রযুক্তি প্রবর্তনের ফলে কাটিয়া নির্ভরযোগ্যতা এবং ফলন উল্লেখযোগ্যভাবে উন্নত হয়েছে।
ভবিষ্যৎ উন্নয়ন এবং নতুন প্রযুক্তি
যদিও ওয়েফার কাটিংয়ে যান্ত্রিক কাটিং প্রযুক্তি এখনও একটি গুরুত্বপূর্ণ স্থান দখল করে আছে, তবুও সেমিকন্ডাক্টর প্রক্রিয়া বিকশিত হওয়ার সাথে সাথে নতুন কাটিং প্রযুক্তি দ্রুত অগ্রসর হচ্ছে। উদাহরণস্বরূপ, তাপীয় লেজার কাটিং প্রযুক্তির প্রয়োগ যান্ত্রিক কাটিংয়ে নির্ভুলতা এবং ত্রুটির সমস্যাগুলির নতুন সমাধান প্রদান করে। এই অ-যোগাযোগ কাটা পদ্ধতি ওয়েফারের উপর শারীরিক চাপ কমায়, চিপিং এবং ফাটলের ঘটনা উল্লেখযোগ্যভাবে হ্রাস করে, বিশেষ করে যখন আরও ভঙ্গুর উপকরণ কাটা হয়। ভবিষ্যতে, উদীয়মান কাটিং কৌশলগুলির সাথে যান্ত্রিক কাটিং প্রযুক্তির একীকরণ সেমিকন্ডাক্টর উৎপাদনকে আরও বিকল্প এবং নমনীয়তা প্রদান করবে, যা উৎপাদন দক্ষতা এবং চিপের গুণমান আরও উন্নত করবে।
উপসংহারে, যদিও যান্ত্রিক কাটিয়া প্রযুক্তির কিছু ত্রুটি রয়েছে, তবুও ক্রমাগত প্রযুক্তিগত উন্নতি এবং নতুন কাটিয়া কৌশলগুলির সাথে এর একীকরণ এটিকে সেমিকন্ডাক্টর উৎপাদনে গুরুত্বপূর্ণ ভূমিকা পালন করতে এবং ভবিষ্যতের প্রক্রিয়াগুলিতে এর প্রতিযোগিতামূলকতা বজায় রাখতে সহায়তা করে।
২.২ লেজার কাটিং প্রযুক্তি
ওয়েফার কাটার ক্ষেত্রে লেজার কাটিং প্রযুক্তি, একটি নতুন পদ্ধতি হিসেবে, উচ্চ নির্ভুলতা, যান্ত্রিক যোগাযোগের ক্ষতির অভাব এবং দ্রুত কাটার ক্ষমতার কারণে সেমিকন্ডাক্টর শিল্পে ধীরে ধীরে ব্যাপক মনোযোগ আকর্ষণ করেছে। এই প্রযুক্তিটি লেজার রশ্মির উচ্চ শক্তি ঘনত্ব এবং ফোকাসিং ক্ষমতা ব্যবহার করে ওয়েফার উপাদানের পৃষ্ঠে একটি ছোট তাপ-প্রভাবিত অঞ্চল তৈরি করে। যখন লেজার রশ্মি ওয়েফারে প্রয়োগ করা হয়, তখন উৎপন্ন তাপীয় চাপ উপাদানটিকে নির্ধারিত স্থানে ভেঙে দেয়, যার ফলে সুনির্দিষ্ট কাটা সম্ভব হয়।
লেজার কাটিং প্রযুক্তির সুবিধা
• উচ্চ নির্ভুলতা: লেজার রশ্মির সুনির্দিষ্ট অবস্থান নির্ধারণ ক্ষমতা মাইক্রোন বা এমনকি ন্যানোমিটার-স্তরের কাটিং নির্ভুলতার অনুমতি দেয়, যা আধুনিক উচ্চ-নির্ভুলতা, উচ্চ-ঘনত্বের সমন্বিত সার্কিট উৎপাদনের প্রয়োজনীয়তা পূরণ করে।
• কোন যান্ত্রিক যোগাযোগ নেই: লেজার কাটিং ওয়েফারের সাথে শারীরিক সংস্পর্শ এড়ায়, যান্ত্রিক কাটিংয়ে সাধারণ সমস্যা যেমন চিপিং এবং ক্র্যাকিং প্রতিরোধ করে, চিপসের ফলন হার এবং নির্ভরযোগ্যতা উল্লেখযোগ্যভাবে উন্নত করে।
• দ্রুত কাটার গতি: লেজার কাটার উচ্চ গতি উৎপাদন দক্ষতা বৃদ্ধিতে অবদান রাখে, যা এটিকে বৃহৎ আকারের, উচ্চ-গতির উৎপাদন পরিস্থিতির জন্য বিশেষভাবে উপযুক্ত করে তোলে।
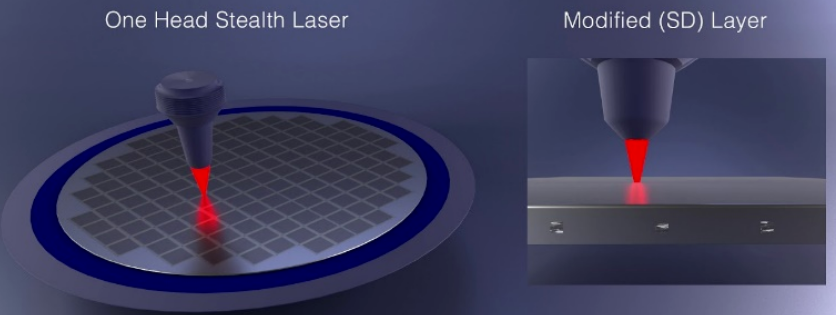
যেসব চ্যালেঞ্জের সম্মুখীন হয়েছেন
• উচ্চ সরঞ্জাম খরচ: লেজার কাটিং সরঞ্জামের জন্য প্রাথমিক বিনিয়োগ বেশি, যা অর্থনৈতিক চাপ তৈরি করে, বিশেষ করে ছোট থেকে মাঝারি আকারের উৎপাদন উদ্যোগের জন্য।
• জটিল প্রক্রিয়া নিয়ন্ত্রণ: লেজার কাটার জন্য শক্তির ঘনত্ব, ফোকাস অবস্থান এবং কাটার গতি সহ বেশ কয়েকটি পরামিতির সুনির্দিষ্ট নিয়ন্ত্রণ প্রয়োজন, যা প্রক্রিয়াটিকে জটিল করে তোলে।
• তাপ-প্রভাবিত অঞ্চলের সমস্যা: যদিও লেজার কাটিং এর যোগাযোগহীন প্রকৃতি যান্ত্রিক ক্ষতি কমায়, তাপ-প্রভাবিত অঞ্চল (HAZ) দ্বারা সৃষ্ট তাপীয় চাপ ওয়েফার উপাদানের বৈশিষ্ট্যগুলিকে নেতিবাচকভাবে প্রভাবিত করতে পারে। এই প্রভাব কমাতে প্রক্রিয়াটির আরও অপ্টিমাইজেশন প্রয়োজন।
প্রযুক্তিগত উন্নয়নের দিকনির্দেশনা
এই চ্যালেঞ্জগুলি মোকাবেলা করার জন্য, গবেষকরা সরঞ্জামের খরচ কমানো, কাটিংয়ের দক্ষতা উন্নত করা এবং প্রক্রিয়া প্রবাহকে অপ্টিমাইজ করার উপর মনোযোগ দিচ্ছেন।
• দক্ষ লেজার এবং অপটিক্যাল সিস্টেম: আরও দক্ষ লেজার এবং উন্নত অপটিক্যাল সিস্টেম তৈরির মাধ্যমে, কাটিংয়ের নির্ভুলতা এবং গতি বৃদ্ধির সাথে সাথে সরঞ্জামের খরচ কমানো সম্ভব।
• প্রক্রিয়া পরামিতি অপ্টিমাইজ করা: তাপ-প্রভাবিত অঞ্চল হ্রাসকারী প্রক্রিয়াগুলিকে উন্নত করার জন্য লেজার এবং ওয়েফার উপকরণের মধ্যে মিথস্ক্রিয়া সম্পর্কে গভীর গবেষণা পরিচালিত হচ্ছে, যার ফলে কাটার মান উন্নত হবে।
• বুদ্ধিমান নিয়ন্ত্রণ ব্যবস্থা: বুদ্ধিমান নিয়ন্ত্রণ প্রযুক্তির বিকাশের লক্ষ্য লেজার কাটার প্রক্রিয়াটিকে স্বয়ংক্রিয় এবং অপ্টিমাইজ করা, এর স্থায়িত্ব এবং ধারাবাহিকতা উন্নত করা।
লেজার কাটিং প্রযুক্তি অতি-পাতলা ওয়েফার এবং উচ্চ-নির্ভুলতা কাটার ক্ষেত্রে বিশেষভাবে কার্যকর। ওয়েফারের আকার বৃদ্ধি এবং সার্কিটের ঘনত্ব বৃদ্ধির সাথে সাথে, ঐতিহ্যবাহী যান্ত্রিক কাটিং পদ্ধতিগুলি আধুনিক সেমিকন্ডাক্টর উৎপাদনের উচ্চ-নির্ভুলতা এবং উচ্চ-দক্ষতার চাহিদা পূরণে লড়াই করে। এর অনন্য সুবিধার কারণে, লেজার কাটিং এই ক্ষেত্রগুলিতে পছন্দের সমাধান হয়ে উঠছে।
যদিও লেজার কাটিং প্রযুক্তি এখনও উচ্চ সরঞ্জাম খরচ এবং প্রক্রিয়া জটিলতার মতো চ্যালেঞ্জের মুখোমুখি, উচ্চ নির্ভুলতা এবং যোগাযোগহীন ক্ষতির ক্ষেত্রে এর অনন্য সুবিধাগুলি এটিকে সেমিকন্ডাক্টর উৎপাদনের উন্নয়নের জন্য একটি গুরুত্বপূর্ণ দিক করে তোলে। লেজার প্রযুক্তি এবং বুদ্ধিমান নিয়ন্ত্রণ ব্যবস্থার অগ্রগতি অব্যাহত থাকায়, লেজার কাটিং ওয়েফার কাটিং দক্ষতা এবং গুণমানকে আরও উন্নত করবে বলে আশা করা হচ্ছে, যা সেমিকন্ডাক্টর শিল্পের ক্রমাগত বিকাশকে চালিত করবে।
২.৩ প্লাজমা কাটিং প্রযুক্তি
প্লাজমা কাটিং প্রযুক্তি, একটি উদীয়মান ওয়েফার ডাইসিং পদ্ধতি হিসেবে, সাম্প্রতিক বছরগুলিতে উল্লেখযোগ্য মনোযোগ আকর্ষণ করেছে। এই প্রযুক্তি উচ্চ-শক্তির প্লাজমা বিম ব্যবহার করে প্লাজমা বিমের শক্তি, গতি এবং কাটিংয়ের পথ নিয়ন্ত্রণ করে ওয়েফারগুলিকে সুনির্দিষ্টভাবে কাটে, সর্বোত্তম কাটিংয়ের ফলাফল অর্জন করে।
কাজের নীতি এবং সুবিধা
প্লাজমা কাটার প্রক্রিয়াটি সরঞ্জাম দ্বারা উৎপন্ন উচ্চ-তাপমাত্রা, উচ্চ-শক্তির প্লাজমা রশ্মির উপর নির্ভর করে। এই রশ্মি খুব অল্প সময়ের মধ্যে ওয়েফার উপাদানকে তার গলনা বা বাষ্পীভবন বিন্দুতে উত্তপ্ত করতে পারে, যা দ্রুত কাটা সম্ভব করে। ঐতিহ্যবাহী যান্ত্রিক বা লেজার কাটার তুলনায়, প্লাজমা কাটা দ্রুত এবং একটি ছোট তাপ-প্রভাবিত অঞ্চল তৈরি করে, যা কাটার সময় ফাটল এবং ক্ষতির ঘটনা কার্যকরভাবে হ্রাস করে।
ব্যবহারিক প্রয়োগে, প্লাজমা কাটিং প্রযুক্তি জটিল আকারের ওয়েফার পরিচালনায় বিশেষভাবে পারদর্শী। এর উচ্চ-শক্তি, সামঞ্জস্যযোগ্য প্লাজমা রশ্মি সহজেই অনিয়মিত আকারের ওয়েফারগুলিকে উচ্চ নির্ভুলতার সাথে কাটতে পারে। অতএব, মাইক্রোইলেকট্রনিক্স উৎপাদনে, বিশেষ করে উচ্চ-মানের চিপগুলির কাস্টমাইজড এবং ছোট-ব্যাচ উৎপাদনে, এই প্রযুক্তি ব্যাপক ব্যবহারের জন্য দুর্দান্ত প্রতিশ্রুতি দেখায়।
চ্যালেঞ্জ এবং সীমাবদ্ধতা
প্লাজমা কাটিং প্রযুক্তির অনেক সুবিধা থাকা সত্ত্বেও, এটি কিছু চ্যালেঞ্জেরও সম্মুখীন হয়।
• জটিল প্রক্রিয়া: প্লাজমা কাটার প্রক্রিয়া জটিল এবং এটি নিশ্চিত করার জন্য উচ্চ-নির্ভুল সরঞ্জাম এবং অভিজ্ঞ অপারেটরদের প্রয়োজনকাটার ক্ষেত্রে নির্ভুলতা এবং স্থায়িত্ব।
• পরিবেশগত নিয়ন্ত্রণ এবং নিরাপত্তা: প্লাজমা রশ্মির উচ্চ-তাপমাত্রা, উচ্চ-শক্তি প্রকৃতির জন্য কঠোর পরিবেশগত নিয়ন্ত্রণ এবং সুরক্ষা ব্যবস্থা প্রয়োজন, যা বাস্তবায়নের জটিলতা এবং ব্যয় বৃদ্ধি করে।
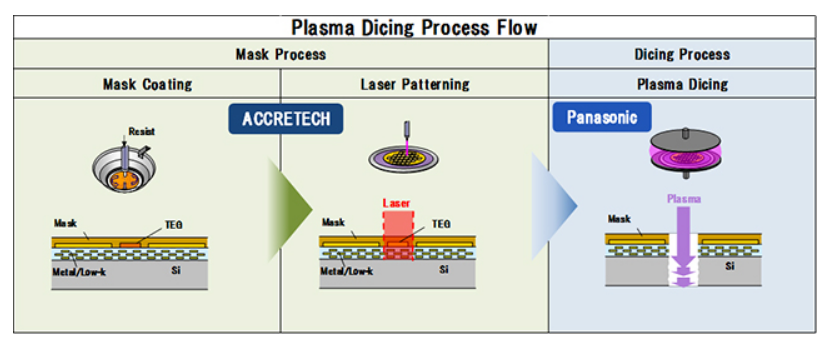
ভবিষ্যতের উন্নয়নের দিকনির্দেশনা
প্রযুক্তিগত অগ্রগতির সাথে সাথে, প্লাজমা কাটার সাথে সম্পর্কিত চ্যালেঞ্জগুলি ধীরে ধীরে কাটিয়ে উঠবে বলে আশা করা হচ্ছে। আরও স্মার্ট এবং স্থিতিশীল কাটিয়া সরঞ্জাম তৈরির মাধ্যমে, ম্যানুয়াল অপারেশনের উপর নির্ভরতা হ্রাস করা যেতে পারে, যার ফলে উৎপাদন দক্ষতা উন্নত হয়। একই সাথে, প্রক্রিয়া পরামিতি এবং কাটিয়া পরিবেশ অপ্টিমাইজ করা নিরাপত্তা ঝুঁকি এবং পরিচালনা খরচ কমাতে সাহায্য করবে।
সেমিকন্ডাক্টর শিল্পে, ওয়েফার কাটিং এবং ডাইসিং প্রযুক্তির উদ্ভাবন শিল্পের উন্নয়নের জন্য অত্যন্ত গুরুত্বপূর্ণ। প্লাজমা কাটিং প্রযুক্তি, এর উচ্চ নির্ভুলতা, দক্ষতা এবং জটিল ওয়েফার আকার পরিচালনা করার ক্ষমতা সহ, এই ক্ষেত্রে একটি গুরুত্বপূর্ণ নতুন খেলোয়াড় হিসাবে আবির্ভূত হয়েছে। যদিও কিছু চ্যালেঞ্জ রয়ে গেছে, তবুও এই সমস্যাগুলি ক্রমাগত প্রযুক্তিগত উদ্ভাবনের মাধ্যমে ধীরে ধীরে সমাধান করা হবে, যা সেমিকন্ডাক্টর উৎপাদনে আরও সম্ভাবনা এবং সুযোগ নিয়ে আসবে।
প্লাজমা কাটিং প্রযুক্তির প্রয়োগের সম্ভাবনা বিশাল, এবং ভবিষ্যতে এটি সেমিকন্ডাক্টর উৎপাদনে আরও গুরুত্বপূর্ণ ভূমিকা পালন করবে বলে আশা করা হচ্ছে। ক্রমাগত প্রযুক্তিগত উদ্ভাবন এবং অপ্টিমাইজেশনের মাধ্যমে, প্লাজমা কাটিং কেবল বিদ্যমান চ্যালেঞ্জগুলিই মোকাবেলা করবে না বরং সেমিকন্ডাক্টর শিল্পের বৃদ্ধির একটি শক্তিশালী চালিকাশক্তিও হয়ে উঠবে।
২.৪ মান হ্রাস এবং প্রভাব বিস্তারকারী বিষয়গুলি
পরবর্তী চিপ প্যাকেজিং, পরীক্ষা, এবং চূড়ান্ত পণ্যের সামগ্রিক কর্মক্ষমতা এবং নির্ভরযোগ্যতার জন্য ওয়েফার কাটার মান অত্যন্ত গুরুত্বপূর্ণ। কাটার সময় যেসব সাধারণ সমস্যা দেখা দেয় তার মধ্যে রয়েছে ফাটল, চিপিং এবং কাটার বিচ্যুতি। এই সমস্যাগুলি একসাথে কাজ করার বিভিন্ন কারণ দ্বারা প্রভাবিত হয়।
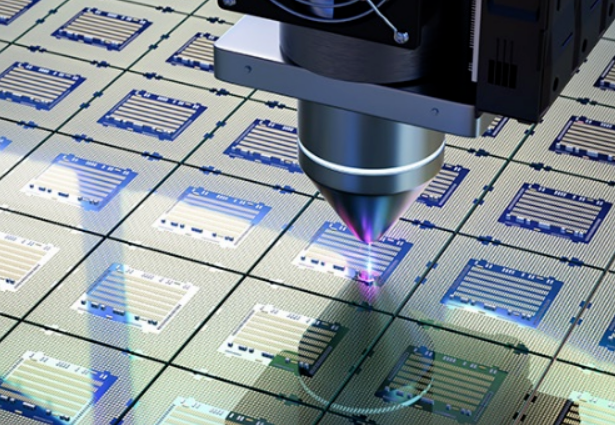
বিভাগ | কন্টেন্ট | প্রভাব |
প্রক্রিয়া পরামিতি | কাটার গতি, ফিড রেট এবং কাটার গভীরতা সরাসরি কাটার প্রক্রিয়ার স্থায়িত্ব এবং নির্ভুলতার উপর প্রভাব ফেলে। অনুপযুক্ত সেটিংস চাপ ঘনত্ব এবং অত্যধিক তাপ-প্রভাবিত অঞ্চলের দিকে পরিচালিত করতে পারে, যার ফলে ফাটল এবং চিপিং হতে পারে। কাঙ্ক্ষিত কাটিংয়ের ফলাফল অর্জনের জন্য ওয়েফার উপাদান, বেধ এবং কাটার প্রয়োজনীয়তার উপর ভিত্তি করে যথাযথভাবে পরামিতিগুলি সামঞ্জস্য করা গুরুত্বপূর্ণ। | সঠিক প্রক্রিয়া পরামিতিগুলি সুনির্দিষ্ট কাটা নিশ্চিত করে এবং ফাটল এবং চিপিংয়ের মতো ত্রুটির ঝুঁকি হ্রাস করে। |
সরঞ্জাম এবং উপাদানের কারণ | -ব্লেডের গুণমান: ব্লেডের উপাদান, কঠোরতা এবং পরিধান প্রতিরোধ ক্ষমতা কাটার প্রক্রিয়ার মসৃণতা এবং কাটা পৃষ্ঠের সমতলতার উপর প্রভাব ফেলে। নিম্নমানের ব্লেড ঘর্ষণ এবং তাপীয় চাপ বৃদ্ধি করে, যার ফলে ফাটল বা চিপিংয়ের সম্ভাবনা থাকে। সঠিক ব্লেডের উপাদান নির্বাচন করা অত্যন্ত গুরুত্বপূর্ণ। -কুল্যান্ট পারফরম্যান্স: কুল্যান্ট কাটার তাপমাত্রা কমাতে, ঘর্ষণ কমাতে এবং ধ্বংসাবশেষ পরিষ্কার করতে সাহায্য করে। অকার্যকর কুল্যান্ট উচ্চ তাপমাত্রা এবং ধ্বংসাবশেষ জমা হতে পারে, যা কাটার মান এবং দক্ষতার উপর প্রভাব ফেলে। দক্ষ এবং পরিবেশ বান্ধব কুল্যান্ট নির্বাচন করা অত্যন্ত গুরুত্বপূর্ণ। | ব্লেডের গুণমান কাটার নির্ভুলতা এবং মসৃণতাকে প্রভাবিত করে। অকার্যকর কুল্যান্টের ফলে কাটার মান এবং দক্ষতা খারাপ হতে পারে, যা সর্বোত্তম কুল্যান্ট ব্যবহারের প্রয়োজনীয়তা তুলে ধরে। |
প্রক্রিয়া নিয়ন্ত্রণ এবং মান পরিদর্শন | -প্রক্রিয়া নিয়ন্ত্রণ: কাটিং প্রক্রিয়ায় স্থিতিশীলতা এবং ধারাবাহিকতা নিশ্চিত করতে মূল কাটিং প্যারামিটারগুলির রিয়েল-টাইম পর্যবেক্ষণ এবং সমন্বয়। -মান পরিদর্শন: কাটার পরের চেহারা পরীক্ষা, মাত্রিক পরিমাপ এবং বৈদ্যুতিক কর্মক্ষমতা পরীক্ষা দ্রুত মানের সমস্যাগুলি সনাক্ত করতে এবং সমাধান করতে সাহায্য করে, কাটার নির্ভুলতা এবং ধারাবাহিকতা উন্নত করে। | সঠিক প্রক্রিয়া নিয়ন্ত্রণ এবং মান পরিদর্শন ধারাবাহিক, উচ্চ-মানের কাটিংয়ের ফলাফল এবং সম্ভাব্য সমস্যাগুলির প্রাথমিক সনাক্তকরণ নিশ্চিত করতে সহায়তা করে। |

কাটিং মান উন্নত করা
কাটিং মান উন্নত করার জন্য একটি ব্যাপক পদ্ধতির প্রয়োজন যা প্রক্রিয়া পরামিতি, সরঞ্জাম এবং উপাদান নির্বাচন, প্রক্রিয়া নিয়ন্ত্রণ এবং পরিদর্শনকে বিবেচনা করে। ক্রমাগত কাটিং প্রযুক্তি পরিমার্জন এবং প্রক্রিয়া পদ্ধতি অপ্টিমাইজ করার মাধ্যমে, ওয়েফার কাটিং এর নির্ভুলতা এবং স্থায়িত্ব আরও উন্নত করা যেতে পারে, যা সেমিকন্ডাক্টর উৎপাদন শিল্পের জন্য আরও নির্ভরযোগ্য প্রযুক্তিগত সহায়তা প্রদান করে।
#03 কাটার পরের হ্যান্ডলিং এবং পরীক্ষা
৩.১ পরিষ্কার এবং শুকানো
চিপের গুণমান এবং পরবর্তী প্রক্রিয়াগুলির মসৃণ অগ্রগতি নিশ্চিত করার জন্য ওয়েফার কাটার পরে পরিষ্কার এবং শুকানোর ধাপগুলি অত্যন্ত গুরুত্বপূর্ণ। এই পর্যায়ে, কাটার সময় উৎপন্ন সিলিকন ধ্বংসাবশেষ, কুল্যান্টের অবশিষ্টাংশ এবং অন্যান্য দূষকগুলি পুঙ্খানুপুঙ্খভাবে অপসারণ করা অপরিহার্য। পরিষ্কারের প্রক্রিয়া চলাকালীন চিপগুলি যাতে ক্ষতিগ্রস্ত না হয় তা নিশ্চিত করা সমানভাবে গুরুত্বপূর্ণ এবং শুকানোর পরে, ক্ষয় বা ইলেক্ট্রোস্ট্যাটিক স্রাবের মতো সমস্যাগুলি প্রতিরোধ করার জন্য চিপের পৃষ্ঠে কোনও আর্দ্রতা না থাকে তা নিশ্চিত করাও সমানভাবে গুরুত্বপূর্ণ।
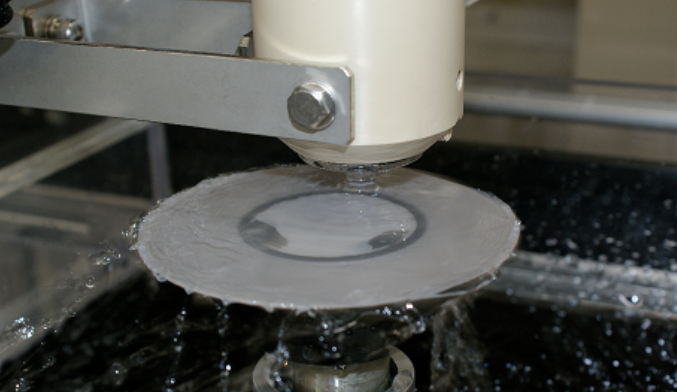
কাটা-পরবর্তী পরিচালনা: পরিষ্কার এবং শুকানোর প্রক্রিয়া
প্রক্রিয়া ধাপ | কন্টেন্ট | প্রভাব |
পরিষ্কারের প্রক্রিয়া | -পদ্ধতি: পরিষ্কারের জন্য বিশেষায়িত পরিষ্কারক এজেন্ট এবং বিশুদ্ধ জল ব্যবহার করুন, আল্ট্রাসনিক বা যান্ত্রিক ব্রাশিং কৌশলের সাথে মিলিত করুন। | দূষণকারী পদার্থের পুঙ্খানুপুঙ্খ অপসারণ নিশ্চিত করে এবং পরিষ্কারের সময় চিপসের ক্ষতি রোধ করে। |
-পরিষ্কারক এজেন্ট নির্বাচন: চিপের ক্ষতি না করে কার্যকর পরিষ্কার নিশ্চিত করতে ওয়েফার উপাদান এবং দূষণকারীর ধরণের উপর ভিত্তি করে নির্বাচন করুন। | কার্যকর পরিষ্কার এবং চিপ সুরক্ষার জন্য সঠিক এজেন্ট নির্বাচন গুরুত্বপূর্ণ। | |
-প্যারামিটার নিয়ন্ত্রণ: অনুপযুক্ত পরিষ্কারের কারণে সৃষ্ট মানের সমস্যা রোধ করতে পরিষ্কারের তাপমাত্রা, সময় এবং পরিষ্কারের দ্রবণের ঘনত্ব কঠোরভাবে নিয়ন্ত্রণ করুন। | নিয়ন্ত্রণগুলি ওয়েফারের ক্ষতি বা দূষণকারী পদার্থ ফেলে যাওয়া এড়াতে সাহায্য করে, যা ধারাবাহিক গুণমান নিশ্চিত করে। | |
শুকানোর প্রক্রিয়া | -ঐতিহ্যবাহী পদ্ধতি: প্রাকৃতিক বাতাসে শুকানো এবং গরম বাতাসে শুকানো, যার দক্ষতা কম এবং স্থির বিদ্যুৎ তৈরি হতে পারে। | এর ফলে শুকানোর সময় ধীর হতে পারে এবং সম্ভাব্য স্থির সমস্যা হতে পারে। |
-আধুনিক প্রযুক্তি: চিপস দ্রুত শুকিয়ে যায় এবং ক্ষতিকারক প্রভাব এড়াতে ভ্যাকুয়াম শুকানোর এবং ইনফ্রারেড শুকানোর মতো উন্নত প্রযুক্তি ব্যবহার করুন। | দ্রুত এবং আরও দক্ষ শুকানোর প্রক্রিয়া, স্থির স্রাব বা আর্দ্রতা-সম্পর্কিত সমস্যার ঝুঁকি হ্রাস করে। | |
সরঞ্জাম নির্বাচন এবং রক্ষণাবেক্ষণ | -সরঞ্জাম নির্বাচন: উচ্চ-কার্যক্ষমতাসম্পন্ন পরিষ্কার এবং শুকানোর মেশিনগুলি প্রক্রিয়াকরণ দক্ষতা উন্নত করে এবং পরিচালনার সময় সম্ভাব্য সমস্যাগুলি সূক্ষ্মভাবে নিয়ন্ত্রণ করে। | উচ্চমানের মেশিনগুলি আরও ভালো প্রক্রিয়াকরণ নিশ্চিত করে এবং পরিষ্কার এবং শুকানোর সময় ত্রুটির সম্ভাবনা কমায়। |
-সরঞ্জাম রক্ষণাবেক্ষণ: নিয়মিত পরিদর্শন এবং রক্ষণাবেক্ষণ নিশ্চিত করে যে সরঞ্জামগুলি সর্বোত্তম কার্যকরী অবস্থায় থাকে, চিপের গুণমান নিশ্চিত করে। | সঠিক রক্ষণাবেক্ষণ সরঞ্জামের ব্যর্থতা রোধ করে, নির্ভরযোগ্য এবং উচ্চ-মানের প্রক্রিয়াকরণ নিশ্চিত করে। |
কাটার পর পরিষ্কার এবং শুকানো
ওয়েফার কাটার পর পরিষ্কার এবং শুকানোর ধাপগুলি জটিল এবং সূক্ষ্ম প্রক্রিয়া যার চূড়ান্ত প্রক্রিয়াকরণের ফলাফল নিশ্চিত করার জন্য একাধিক বিষয়ের যত্ন সহকারে বিবেচনা করা প্রয়োজন। বৈজ্ঞানিক পদ্ধতি এবং কঠোর পদ্ধতি ব্যবহার করে, প্রতিটি চিপ সর্বোত্তম অবস্থায় পরবর্তী প্যাকেজিং এবং পরীক্ষার পর্যায়ে প্রবেশ করে তা নিশ্চিত করা সম্ভব।
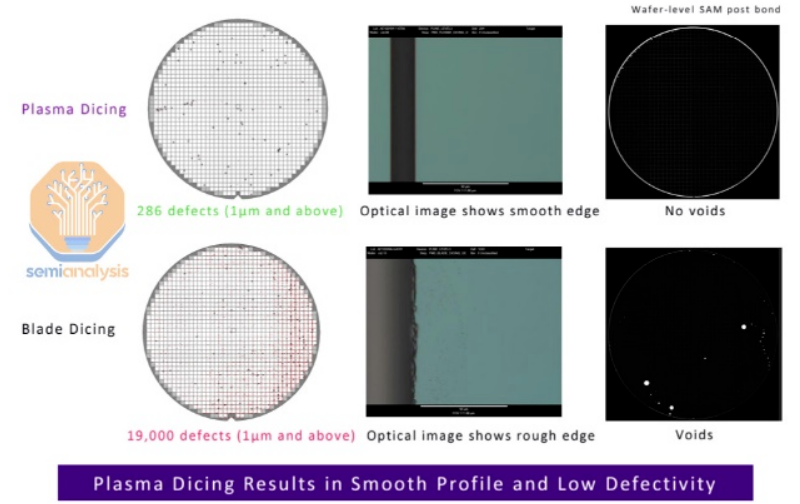
কাটা-পরবর্তী পরিদর্শন এবং পরীক্ষা
ধাপ | কন্টেন্ট | প্রভাব |
পরিদর্শন পদক্ষেপ | ১.চাক্ষুষ পরিদর্শন: চিপের পৃষ্ঠে ফাটল, চিপিং বা দূষণের মতো দৃশ্যমান ত্রুটিগুলি পরীক্ষা করার জন্য ভিজ্যুয়াল বা স্বয়ংক্রিয় পরিদর্শন সরঞ্জাম ব্যবহার করুন। অপচয় এড়াতে দ্রুত শারীরিকভাবে ক্ষতিগ্রস্ত চিপগুলি সনাক্ত করুন। | প্রক্রিয়ার শুরুতেই ত্রুটিপূর্ণ চিপগুলি সনাক্ত এবং নির্মূল করতে সাহায্য করে, উপাদানের ক্ষতি হ্রাস করে। |
২.আকার পরিমাপ: চিপের মাত্রা সঠিকভাবে পরিমাপ করার জন্য নির্ভুল পরিমাপ যন্ত্র ব্যবহার করুন, যাতে কাটার আকার ডিজাইনের নির্দিষ্টকরণ পূরণ করে এবং কর্মক্ষমতা সংক্রান্ত সমস্যা বা প্যাকেজিং অসুবিধা প্রতিরোধ করে। | নিশ্চিত করে যে চিপগুলি প্রয়োজনীয় আকারের সীমার মধ্যে রয়েছে, কর্মক্ষমতা হ্রাস বা সমাবেশ সমস্যা প্রতিরোধ করে। | |
৩.বৈদ্যুতিক কর্মক্ষমতা পরীক্ষা: অ-সম্মতিপ্রাপ্ত চিপগুলি সনাক্ত করতে এবং কেবলমাত্র কর্মক্ষমতা-যোগ্য চিপগুলি পরবর্তী পর্যায়ে যাওয়ার জন্য প্রতিরোধ, ক্যাপাসিট্যান্স এবং ইন্ডাক্ট্যান্সের মতো গুরুত্বপূর্ণ বৈদ্যুতিক পরামিতিগুলি মূল্যায়ন করুন। | প্রক্রিয়াটিতে কেবল কার্যকরী এবং কর্মক্ষমতা-পরীক্ষিত চিপগুলি এগিয়ে যাওয়ার বিষয়টি নিশ্চিত করে, পরবর্তী পর্যায়ে ব্যর্থতার ঝুঁকি হ্রাস করে। | |
পরীক্ষার ধাপ | ১.কার্যকরী পরীক্ষা: চিপের মৌলিক কার্যকারিতা উদ্দেশ্য অনুযায়ী কাজ করছে কিনা তা যাচাই করুন, কার্যকরী অস্বাভাবিকতাযুক্ত চিপগুলি সনাক্ত এবং নির্মূল করুন। | পরবর্তী পর্যায়ে যাওয়ার আগে চিপগুলি মৌলিক কর্মক্ষম প্রয়োজনীয়তা পূরণ করে তা নিশ্চিত করে। |
২.নির্ভরযোগ্যতা পরীক্ষা: দীর্ঘস্থায়ী ব্যবহার বা কঠোর পরিবেশে চিপের কর্মক্ষমতা স্থিতিশীলতা মূল্যায়ন করুন, সাধারণত উচ্চ-তাপমাত্রার বার্ধক্য, নিম্ন-তাপমাত্রা পরীক্ষা এবং বাস্তব-বিশ্বের চরম পরিস্থিতি অনুকরণ করার জন্য আর্দ্রতা পরীক্ষা জড়িত। | নিশ্চিত করে যে চিপগুলি বিভিন্ন পরিবেশগত পরিস্থিতিতে নির্ভরযোগ্যভাবে কাজ করতে পারে, পণ্যের দীর্ঘায়ু এবং স্থায়িত্ব উন্নত করে। | |
৩.সামঞ্জস্যতা পরীক্ষা: চিপটি অন্যান্য উপাদান বা সিস্টেমের সাথে সঠিকভাবে কাজ করছে কিনা তা যাচাই করুন, নিশ্চিত করুন যে অসঙ্গতির কারণে কোনও ত্রুটি বা কর্মক্ষমতা হ্রাস পাচ্ছে না। | সামঞ্জস্যের সমস্যা প্রতিরোধ করে বাস্তব-বিশ্বের অ্যাপ্লিকেশনগুলিতে মসৃণ অপারেশন নিশ্চিত করে। |
৩.৩ প্যাকেজিং এবং স্টোরেজ
ওয়েফার কাটার পর, চিপগুলি সেমিকন্ডাক্টর উৎপাদন প্রক্রিয়ার একটি গুরুত্বপূর্ণ আউটপুট, এবং তাদের প্যাকেজিং এবং স্টোরেজ পর্যায়গুলিও সমানভাবে গুরুত্বপূর্ণ। সঠিক প্যাকেজিং এবং স্টোরেজ ব্যবস্থা কেবল পরিবহন এবং স্টোরেজের সময় চিপগুলির সুরক্ষা এবং স্থিতিশীলতা নিশ্চিত করার জন্যই নয়, বরং পরবর্তী উৎপাদন, পরীক্ষা এবং প্যাকেজিং পর্যায়ে শক্তিশালী সহায়তা প্রদানের জন্যও অপরিহার্য।
পরিদর্শন এবং পরীক্ষার পর্যায়ের সারসংক্ষেপ:
ওয়েফার কাটার পর চিপসের পরিদর্শন এবং পরীক্ষার ধাপগুলি বিভিন্ন দিককে অন্তর্ভুক্ত করে, যার মধ্যে রয়েছে ভিজ্যুয়াল পরিদর্শন, আকার পরিমাপ, বৈদ্যুতিক কর্মক্ষমতা পরীক্ষা, কার্যকরী পরীক্ষা, নির্ভরযোগ্যতা পরীক্ষা এবং সামঞ্জস্য পরীক্ষা। এই ধাপগুলি আন্তঃসংযুক্ত এবং পরিপূরক, পণ্যের গুণমান এবং নির্ভরযোগ্যতা নিশ্চিত করার জন্য একটি শক্ত বাধা তৈরি করে। কঠোর পরিদর্শন এবং পরীক্ষার পদ্ধতির মাধ্যমে, সম্ভাব্য সমস্যাগুলি চিহ্নিত করা এবং তাৎক্ষণিকভাবে সমাধান করা যেতে পারে, নিশ্চিত করে যে চূড়ান্ত পণ্য গ্রাহকের প্রয়োজনীয়তা এবং প্রত্যাশা পূরণ করে।
দিক | কন্টেন্ট |
প্যাকেজিং ব্যবস্থা | ১.অ্যান্টি-স্ট্যাটিক: প্যাকেজিং উপকরণগুলিতে চমৎকার অ্যান্টি-স্ট্যাটিক বৈশিষ্ট্য থাকা উচিত যাতে স্ট্যাটিক বিদ্যুৎ ডিভাইসের ক্ষতি না করে বা তাদের কর্মক্ষমতা প্রভাবিত না করে। |
২.আর্দ্রতা-প্রতিরোধী: আর্দ্রতার কারণে ক্ষয় এবং বৈদ্যুতিক কর্মক্ষমতার অবনতি রোধ করার জন্য প্যাকেজিং উপকরণগুলিতে ভালো আর্দ্রতা প্রতিরোধ ক্ষমতা থাকা উচিত। | |
৩.আঘাত-প্রতিরোধী: পরিবহনের সময় কম্পন এবং আঘাত থেকে চিপগুলিকে রক্ষা করার জন্য প্যাকেজিং উপকরণগুলি কার্যকর শক শোষণ প্রদান করবে। | |
স্টোরেজ পরিবেশ | ১.আর্দ্রতা নিয়ন্ত্রণ: অতিরিক্ত আর্দ্রতার কারণে আর্দ্রতা শোষণ এবং ক্ষয় রোধ করতে অথবা কম আর্দ্রতার কারণে স্থির সমস্যা রোধ করতে যথাযথ পরিসরের মধ্যে আর্দ্রতা কঠোরভাবে নিয়ন্ত্রণ করুন। |
২.পরিচ্ছন্নতা: ধুলো এবং অপরিষ্কার পদার্থ দ্বারা চিপস দূষিত না হওয়ার জন্য একটি পরিষ্কার সংরক্ষণাগার পরিবেশ বজায় রাখুন। | |
৩.তাপমাত্রা নিয়ন্ত্রণ: কম তাপমাত্রার কারণে অতিরিক্ত তাপ বা ঘনীভবনের সমস্যা রোধ করতে যুক্তিসঙ্গত তাপমাত্রার পরিসর নির্ধারণ করুন এবং তাপমাত্রার স্থিতিশীলতা বজায় রাখুন। | |
নিয়মিত পরিদর্শন | সময়মতো সম্ভাব্য সমস্যাগুলি সনাক্ত এবং সমাধানের জন্য ভিজ্যুয়াল পরিদর্শন, আকার পরিমাপ এবং বৈদ্যুতিক কর্মক্ষমতা পরীক্ষা ব্যবহার করে নিয়মিতভাবে সঞ্চিত চিপগুলি পরিদর্শন এবং মূল্যায়ন করুন। সংরক্ষণের সময় এবং অবস্থার উপর ভিত্তি করে, চিপগুলি সর্বোত্তম অবস্থায় ব্যবহার করা হচ্ছে তা নিশ্চিত করার জন্য ব্যবহারের পরিকল্পনা করুন। |
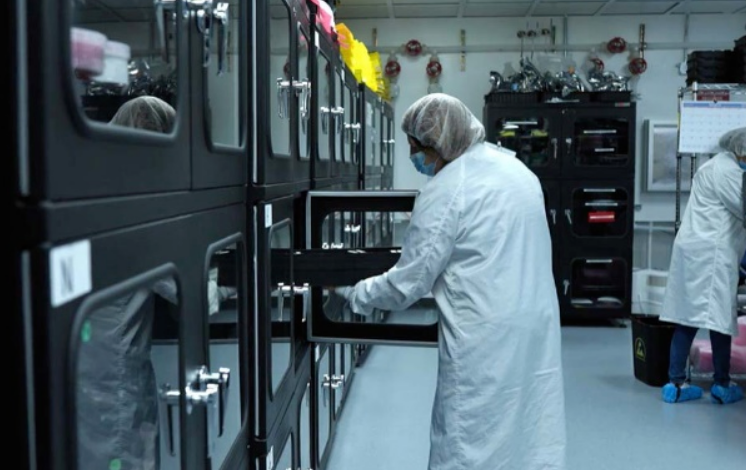
ওয়েফার ডাইসিং প্রক্রিয়ার সময় মাইক্রোক্র্যাক এবং ক্ষতির সমস্যা সেমিকন্ডাক্টর উৎপাদনে একটি গুরুত্বপূর্ণ চ্যালেঞ্জ। কাটার চাপ এই ঘটনার প্রাথমিক কারণ, কারণ এটি ওয়েফার পৃষ্ঠে ছোট ছোট ফাটল এবং ক্ষতির সৃষ্টি করে, যার ফলে উৎপাদন খরচ বৃদ্ধি পায় এবং পণ্যের গুণমান হ্রাস পায়।
এই চ্যালেঞ্জ মোকাবেলা করার জন্য, কাটার চাপ কমানো এবং অপ্টিমাইজড কাটিং কৌশল, সরঞ্জাম এবং শর্তাবলী বাস্তবায়ন করা অত্যন্ত গুরুত্বপূর্ণ। ব্লেডের উপাদান, কাটার গতি, চাপ এবং শীতলকরণ পদ্ধতির মতো বিষয়গুলির প্রতি যত্নশীল মনোযোগ মাইক্রোক্র্যাক গঠন কমাতে এবং প্রক্রিয়াটির সামগ্রিক ফলন উন্নত করতে সাহায্য করতে পারে। উপরন্তু, লেজার ডাইসিংয়ের মতো আরও উন্নত কাটিং প্রযুক্তির উপর চলমান গবেষণা এই সমস্যাগুলি আরও কমানোর উপায়গুলি অন্বেষণ করছে।
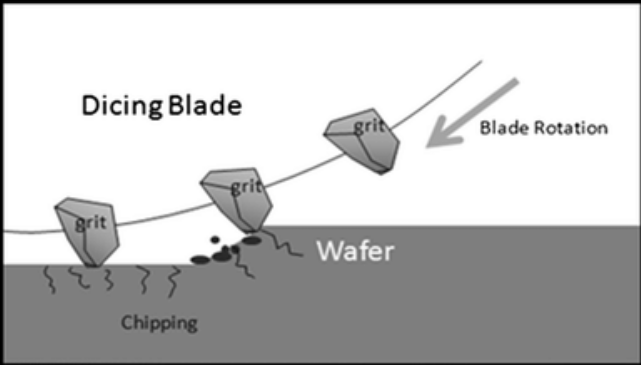
ভঙ্গুর উপাদান হিসেবে, ওয়েফারগুলি যান্ত্রিক, তাপীয় বা রাসায়নিক চাপের শিকার হলে অভ্যন্তরীণ কাঠামোগত পরিবর্তনের ঝুঁকিতে থাকে, যার ফলে মাইক্রোফাটল তৈরি হয়। যদিও এই ফাটলগুলি তাৎক্ষণিকভাবে লক্ষণীয় নাও হতে পারে, তবে উৎপাদন প্রক্রিয়া এগিয়ে যাওয়ার সাথে সাথে এগুলি প্রসারিত হতে পারে এবং আরও গুরুতর ক্ষতি করতে পারে। পরবর্তী প্যাকেজিং এবং পরীক্ষার পর্যায়ে এই সমস্যাটি বিশেষভাবে সমস্যাযুক্ত হয়ে ওঠে, যেখানে তাপমাত্রার ওঠানামা এবং অতিরিক্ত যান্ত্রিক চাপ এই মাইক্রোফাটলগুলিকে দৃশ্যমান ফ্র্যাকচারে পরিণত করতে পারে, যা চিপ ব্যর্থতার কারণ হতে পারে।
এই ঝুঁকি কমাতে, কাটার গতি, চাপ এবং তাপমাত্রার মতো পরামিতিগুলি অপ্টিমাইজ করে সাবধানে কাটার প্রক্রিয়া নিয়ন্ত্রণ করা অপরিহার্য। লেজার ডাইসিংয়ের মতো কম আক্রমণাত্মক কাটিয়া পদ্ধতি ব্যবহার করে ওয়েফারের উপর যান্ত্রিক চাপ কমানো যায় এবং মাইক্রোক্র্যাকের গঠন কমানো যায়। উপরন্তু, ওয়েফার ডাইসিং প্রক্রিয়ার সময় ইনফ্রারেড স্ক্যানিং বা এক্স-রে ইমেজিংয়ের মতো উন্নত পরিদর্শন পদ্ধতি প্রয়োগ করলে এই প্রাথমিক পর্যায়ের ফাটলগুলি আরও ক্ষতির কারণ হওয়ার আগে সনাক্ত করা সম্ভব।
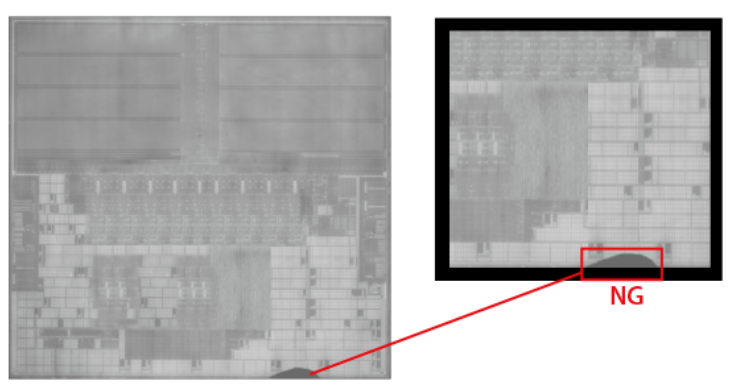
ডাইসিং প্রক্রিয়ায় ওয়েফার পৃষ্ঠের ক্ষতি একটি গুরুত্বপূর্ণ উদ্বেগের বিষয়, কারণ এটি চিপের কর্মক্ষমতা এবং নির্ভরযোগ্যতার উপর সরাসরি প্রভাব ফেলতে পারে। এই ধরনের ক্ষতি কাটিং টুলের অনুপযুক্ত ব্যবহার, ভুল কাটিং প্যারামিটার বা ওয়েফারের মধ্যেই অন্তর্নিহিত উপাদানের ত্রুটির কারণে হতে পারে। কারণ যাই হোক না কেন, এই ক্ষতিগুলি সার্কিটের বৈদ্যুতিক প্রতিরোধ বা ক্যাপাসিট্যান্সে পরিবর্তন আনতে পারে, যা সামগ্রিক কর্মক্ষমতাকে প্রভাবিত করে।
এই সমস্যাগুলি সমাধানের জন্য, দুটি মূল কৌশল অন্বেষণ করা হচ্ছে:
1. কাটিয়া সরঞ্জাম এবং পরামিতি অপ্টিমাইজ করা: ধারালো ব্লেড ব্যবহার করে, কাটার গতি সামঞ্জস্য করে এবং কাটার গভীরতা পরিবর্তন করে, কাটার প্রক্রিয়ার সময় চাপের ঘনত্ব কমানো যায়, ফলে ক্ষতির সম্ভাবনা হ্রাস পায়।
২. নতুন কাটিং প্রযুক্তি অন্বেষণ: লেজার কাটিং এবং প্লাজমা কাটার মতো উন্নত কৌশলগুলি উন্নত নির্ভুলতা প্রদান করে এবং ওয়েফারের ক্ষতির মাত্রা কমিয়ে আনে। ওয়েফারের উপর তাপীয় এবং যান্ত্রিক চাপ কমিয়ে উচ্চ কাটিংয়ের নির্ভুলতা অর্জনের উপায় খুঁজে বের করার জন্য এই প্রযুক্তিগুলি অধ্যয়ন করা হচ্ছে।
তাপীয় প্রভাব এলাকা এবং কর্মক্ষমতার উপর এর প্রভাব
লেজার এবং প্লাজমা কাটার মতো তাপীয় কাটিয়া প্রক্রিয়াগুলিতে, উচ্চ তাপমাত্রা অনিবার্যভাবে ওয়েফারের পৃষ্ঠে একটি তাপীয় প্রভাব অঞ্চল তৈরি করে। এই অঞ্চলটি, যেখানে তাপমাত্রার গ্রেডিয়েন্ট উল্লেখযোগ্য, উপাদানের বৈশিষ্ট্যগুলিকে পরিবর্তন করতে পারে, যা চিপের চূড়ান্ত কর্মক্ষমতাকে প্রভাবিত করে।
তাপীয় প্রভাবিত অঞ্চল (TAZ) এর প্রভাব:
স্ফটিক গঠন পরিবর্তন: উচ্চ তাপমাত্রায়, ওয়েফার উপাদানের মধ্যে থাকা পরমাণুগুলি পুনর্বিন্যাস করতে পারে, যার ফলে স্ফটিক কাঠামোতে বিকৃতি দেখা দেয়। এই বিকৃতি উপাদানটিকে দুর্বল করে, এর যান্ত্রিক শক্তি এবং স্থায়িত্ব হ্রাস করে, যা ব্যবহারের সময় চিপ ব্যর্থতার ঝুঁকি বাড়ায়।
বৈদ্যুতিক বৈশিষ্ট্যের পরিবর্তন: উচ্চ তাপমাত্রা অর্ধপরিবাহী পদার্থের বাহক ঘনত্ব এবং গতিশীলতা পরিবর্তন করতে পারে, যা চিপের বৈদ্যুতিক পরিবাহিতা এবং কারেন্ট ট্রান্সমিশন দক্ষতাকে প্রভাবিত করে। এই পরিবর্তনগুলি চিপের কর্মক্ষমতা হ্রাস করতে পারে, যা সম্ভাব্যভাবে এটিকে তার উদ্দেশ্যের জন্য অনুপযুক্ত করে তুলতে পারে।
এই প্রভাবগুলি প্রশমিত করার জন্য, কাটার সময় তাপমাত্রা নিয়ন্ত্রণ করা, কাটার পরামিতিগুলি অপ্টিমাইজ করা এবং কুলিং জেট বা প্রক্রিয়াকরণ পরবর্তী চিকিত্সার মতো পদ্ধতিগুলি অন্বেষণ করা তাপীয় প্রভাবের পরিমাণ কমাতে এবং উপাদানের অখণ্ডতা বজায় রাখার জন্য অপরিহার্য কৌশল।
সামগ্রিকভাবে, ওয়েফার ডাইসিং প্রযুক্তিতে মাইক্রোক্র্যাক এবং তাপীয় প্রভাব অঞ্চল উভয়ই গুরুত্বপূর্ণ চ্যালেঞ্জ। অর্ধপরিবাহী পণ্যের মান উন্নত করতে এবং তাদের বাজার প্রতিযোগিতামূলকতা বাড়াতে প্রযুক্তিগত অগ্রগতি এবং মান নিয়ন্ত্রণ ব্যবস্থার পাশাপাশি অব্যাহত গবেষণা প্রয়োজন হবে।
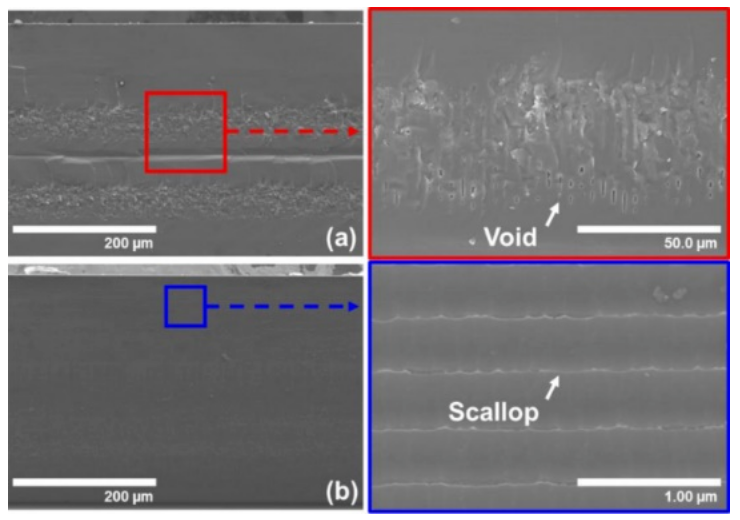
তাপীয় প্রভাব অঞ্চল নিয়ন্ত্রণের ব্যবস্থা:
কাটিং প্রক্রিয়ার পরামিতি অপ্টিমাইজ করা: কাটার গতি এবং শক্তি হ্রাস করলে তাপীয় প্রভাব অঞ্চল (TAZ) এর আকার কার্যকরভাবে হ্রাস করা যায়। এটি কাটার প্রক্রিয়া চলাকালীন উৎপন্ন তাপের পরিমাণ নিয়ন্ত্রণে সাহায্য করে, যা সরাসরি ওয়েফারের উপাদান বৈশিষ্ট্যগুলিকে প্রভাবিত করে।
উন্নত কুলিং প্রযুক্তি: তরল নাইট্রোজেন কুলিং এবং মাইক্রোফ্লুইডিক কুলিং এর মতো প্রযুক্তির প্রয়োগ তাপীয় প্রভাব অঞ্চলের পরিসরকে উল্লেখযোগ্যভাবে সীমিত করতে পারে। এই কুলিং পদ্ধতিগুলি তাপকে আরও দক্ষতার সাথে অপচয় করতে সাহায্য করে, এইভাবে ওয়েফারের উপাদানগত বৈশিষ্ট্যগুলি সংরক্ষণ করে এবং তাপীয় ক্ষতি কমিয়ে দেয়।
উপাদান নির্বাচন: গবেষকরা কার্বন ন্যানোটিউব এবং গ্রাফিনের মতো নতুন উপকরণগুলি অন্বেষণ করছেন, যার চমৎকার তাপ পরিবাহিতা এবং যান্ত্রিক শক্তি রয়েছে। এই উপকরণগুলি চিপগুলির সামগ্রিক কর্মক্ষমতা উন্নত করার সাথে সাথে তাপীয় প্রভাব অঞ্চল হ্রাস করতে পারে।
সংক্ষেপে, যদিও তাপীয় প্রভাব অঞ্চল তাপীয় কাটিয়া প্রযুক্তির একটি অনিবার্য পরিণতি, এটি অপ্টিমাইজড প্রক্রিয়াকরণ কৌশল এবং উপাদান নির্বাচনের মাধ্যমে কার্যকরভাবে নিয়ন্ত্রণ করা যেতে পারে। ভবিষ্যতের গবেষণা সম্ভবত আরও দক্ষ এবং সুনির্দিষ্ট ওয়েফার ডাইসিং অর্জনের জন্য তাপীয় কাটিয়া প্রক্রিয়াগুলিকে সূক্ষ্ম-টিউনিং এবং স্বয়ংক্রিয় করার উপর দৃষ্টি নিবদ্ধ করবে।

ভারসাম্য কৌশল:
ওয়েফার ডাইসিং প্রযুক্তিতে ওয়েফারের ফলন এবং উৎপাদন দক্ষতার মধ্যে সর্বোত্তম ভারসাম্য অর্জন করা একটি ক্রমাগত চ্যালেঞ্জ। যুক্তিসঙ্গত উৎপাদন কৌশল এবং প্রক্রিয়া পরামিতি তৈরি করতে, নির্মাতাদের বাজারের চাহিদা, উৎপাদন খরচ এবং পণ্যের গুণমানের মতো একাধিক বিষয় বিবেচনা করতে হবে। একই সাথে, উন্নত কাটিয়া সরঞ্জাম প্রবর্তন, অপারেটর দক্ষতা উন্নত করা এবং কাঁচামালের মান নিয়ন্ত্রণ বৃদ্ধি করা উৎপাদন দক্ষতা বৃদ্ধির সাথে সাথে ফলন বজায় রাখা বা এমনকি উন্নত করার জন্য অপরিহার্য।
ভবিষ্যতের চ্যালেঞ্জ এবং সুযোগ:
সেমিকন্ডাক্টর প্রযুক্তির অগ্রগতির সাথে সাথে, ওয়েফার কাটিং নতুন চ্যালেঞ্জ এবং সুযোগের মুখোমুখি হচ্ছে। চিপের আকার সঙ্কুচিত হওয়ার সাথে সাথে এবং ইন্টিগ্রেশন বৃদ্ধির সাথে সাথে, কাটিংয়ের নির্ভুলতা এবং মানের চাহিদা উল্লেখযোগ্যভাবে বৃদ্ধি পায়। একই সাথে, উদীয়মান প্রযুক্তিগুলি ওয়েফার কাটিং কৌশলগুলির বিকাশের জন্য নতুন ধারণা প্রদান করে। নির্মাতাদের বাজারের গতিশীলতা এবং প্রযুক্তিগত প্রবণতার সাথে সামঞ্জস্যপূর্ণ থাকতে হবে, বাজারের পরিবর্তন এবং প্রযুক্তিগত চাহিদা পূরণের জন্য উৎপাদন কৌশল এবং প্রক্রিয়া পরামিতিগুলিকে ক্রমাগত সামঞ্জস্য এবং অপ্টিমাইজ করতে হবে।
উপসংহারে, বাজারের চাহিদা, উৎপাদন খরচ এবং পণ্যের গুণমান বিবেচনা করে এবং উন্নত সরঞ্জাম ও প্রযুক্তি প্রবর্তন করে, অপারেটর দক্ষতা বৃদ্ধি করে এবং কাঁচামাল নিয়ন্ত্রণ জোরদার করে, নির্মাতারা ওয়েফার ডাইসিংয়ের সময় ওয়েফারের ফলন এবং উৎপাদন দক্ষতার মধ্যে সর্বোত্তম ভারসাম্য অর্জন করতে পারে, যার ফলে দক্ষ এবং উচ্চ-মানের সেমিকন্ডাক্টর পণ্য উৎপাদন সম্ভব হয়।
ভবিষ্যতের আভাস:
দ্রুত প্রযুক্তিগত অগ্রগতির সাথে সাথে, সেমিকন্ডাক্টর প্রযুক্তি অভূতপূর্ব গতিতে এগিয়ে চলেছে। সেমিকন্ডাক্টর উৎপাদনের ক্ষেত্রে একটি গুরুত্বপূর্ণ পদক্ষেপ হিসেবে, ওয়েফার কাটিং প্রযুক্তি উত্তেজনাপূর্ণ নতুন উন্নয়নের জন্য প্রস্তুত। ভবিষ্যতের দিকে তাকালে, ওয়েফার কাটিং প্রযুক্তি নির্ভুলতা, দক্ষতা এবং খরচের ক্ষেত্রে উল্লেখযোগ্য উন্নতি অর্জন করবে বলে আশা করা হচ্ছে, যা সেমিকন্ডাক্টর শিল্পের অব্যাহত প্রবৃদ্ধিতে নতুন প্রাণশক্তি সঞ্চার করবে।
নির্ভুলতা বৃদ্ধি:
উচ্চতর নির্ভুলতার সাধনায়, ওয়েফার কাটিং প্রযুক্তি ক্রমাগত বিদ্যমান প্রক্রিয়াগুলির সীমা অতিক্রম করবে। কাটিং প্রক্রিয়ার ভৌত এবং রাসায়নিক প্রক্রিয়াগুলি গভীরভাবে অধ্যয়ন করে এবং কাটিং পরামিতিগুলিকে সঠিকভাবে নিয়ন্ত্রণ করে, ক্রমবর্ধমান জটিল সার্কিট ডিজাইনের প্রয়োজনীয়তা পূরণের জন্য সূক্ষ্ম কাটিং ফলাফল অর্জন করা হবে। উপরন্তু, নতুন উপকরণ এবং কাটিং পদ্ধতির অন্বেষণ ফলন এবং গুণমান উল্লেখযোগ্যভাবে উন্নত করবে।
দক্ষতা বৃদ্ধি:
নতুন ওয়েফার কাটিং সরঞ্জামগুলি স্মার্ট এবং স্বয়ংক্রিয় নকশার উপর জোর দেবে। উন্নত নিয়ন্ত্রণ ব্যবস্থা এবং অ্যালগরিদম প্রবর্তনের ফলে সরঞ্জামগুলি বিভিন্ন উপকরণ এবং নকশার প্রয়োজনীয়তার সাথে সামঞ্জস্যপূর্ণভাবে কাটিং পরামিতিগুলি স্বয়ংক্রিয়ভাবে সামঞ্জস্য করতে সক্ষম হবে, যার ফলে উৎপাদন দক্ষতা উল্লেখযোগ্যভাবে উন্নত হবে। মাল্টি-ওয়েফার কাটিং প্রযুক্তি এবং দ্রুত ব্লেড প্রতিস্থাপন সিস্টেমের মতো উদ্ভাবনগুলি দক্ষতা বৃদ্ধিতে গুরুত্বপূর্ণ ভূমিকা পালন করবে।
খরচ কমানো:
ওয়েফার কাটিং প্রযুক্তির উন্নয়নের জন্য খরচ কমানো একটি গুরুত্বপূর্ণ দিক। নতুন উপকরণ এবং কাটিং পদ্ধতি উদ্ভাবনের সাথে সাথে, সরঞ্জামের খরচ এবং রক্ষণাবেক্ষণ ব্যয় কার্যকরভাবে নিয়ন্ত্রণ করা হবে বলে আশা করা হচ্ছে। উপরন্তু, উৎপাদন প্রক্রিয়াগুলি অপ্টিমাইজ করা এবং স্ক্র্যাপের হার হ্রাস করা উৎপাদনের সময় অপচয় আরও কমাবে, যার ফলে সামগ্রিক উৎপাদন খরচ হ্রাস পাবে।
স্মার্ট ম্যানুফ্যাকচারিং এবং আইওটি:
স্মার্ট ম্যানুফ্যাকচারিং এবং ইন্টারনেট অফ থিংস (IoT) প্রযুক্তির একীকরণ ওয়েফার কাটিং প্রযুক্তিতে রূপান্তরমূলক পরিবর্তন আনবে। ডিভাইসগুলির মধ্যে আন্তঃসংযোগ এবং ডেটা ভাগাভাগির মাধ্যমে, উৎপাদন প্রক্রিয়ার প্রতিটি ধাপ রিয়েল টাইমে পর্যবেক্ষণ এবং অপ্টিমাইজ করা যেতে পারে। এটি কেবল উৎপাদন দক্ষতা এবং পণ্যের মান উন্নত করে না বরং কোম্পানিগুলিকে আরও সঠিক বাজার পূর্বাভাস এবং সিদ্ধান্ত গ্রহণের সহায়তা প্রদান করে।
ভবিষ্যতে, ওয়েফার কাটিং প্রযুক্তি নির্ভুলতা, দক্ষতা এবং খরচের ক্ষেত্রে উল্লেখযোগ্য অগ্রগতি সাধন করবে। এই অগ্রগতিগুলি সেমিকন্ডাক্টর শিল্পের অব্যাহত বিকাশকে চালিত করবে এবং মানব সমাজে আরও প্রযুক্তিগত উদ্ভাবন এবং সুবিধা নিয়ে আসবে।
পোস্টের সময়: নভেম্বর-১৯-২০২৪